Masterio spraying systems – a short story, how it is and how it used to be
Spraying systems are most often used in edgebanders to maximize efficiency and pace of production. Why are those systems used to apply OK fluids and what the purpose of such process was described here. In this passage we will focus solely on the evolution of Masterio spraying systems and characterize the major differences between them.
Although spraying points are installed in several models of edgebanders, most models haven’t got such equipment. That is why we created Masterio spraying systems, which can solve this problem without much interference with the machine.
Very often we install our spraying systems on machines that already had stock spraying points. It is because over the years the stock systems stop working properly and Masterio solutions are currently more advanced than factory solutions.
Our systems give much more potential for spray adjustment. They can signal fluid shortage. The nozzles are more economical, enable better fluid application regulation and even counting of application cycles and spraying offset on the format. Our current system is named SN 5, but it all has started a long time ago with SN 1 model.
Masterio SN 1 spraying system
When we first have introduced this system years ago, it was game-changing at that time, but now we know that it had taught us the most and we have made many improvements in the next models.
SN 1 could be implemented at any spraying point (before milling cutter, on the roller, behind the pressure rollers, in front of the polishers) but could attend only one spraying point. It meant that if one wanted all four spraying points on a machine, one would need four spraying systems. It meant quadrupling all the essential installation elements – four 230 V power points, four mounting points on the machine, four compressed air inputs etc. What is more, it could apply fluids only when the format was directly under the sensor. It had no emergency switch that prevented constant fluid application when the format stopped under the sensor, e.g. due to production line halt.
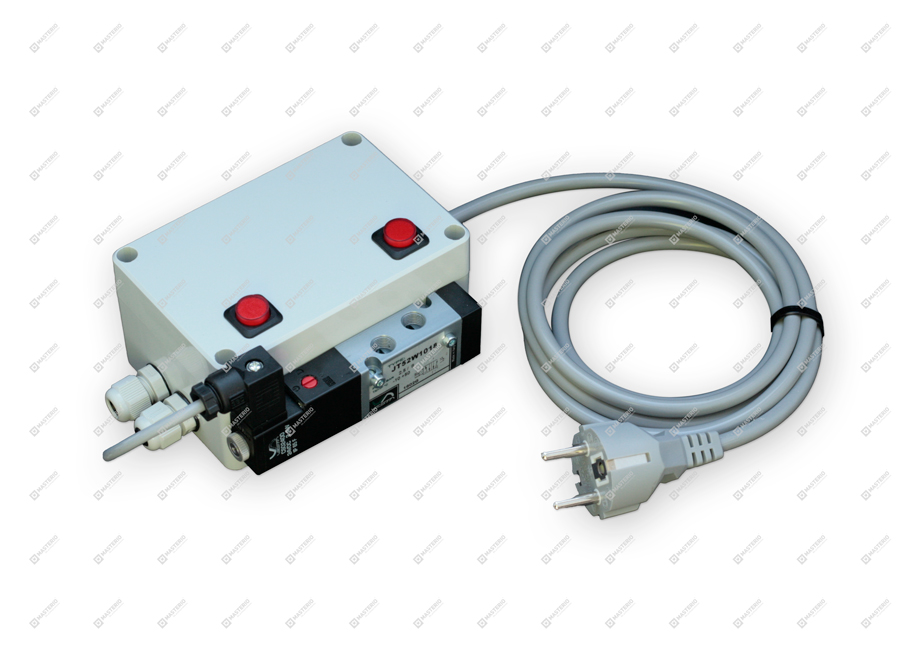
Masterio SN 2 spraying system
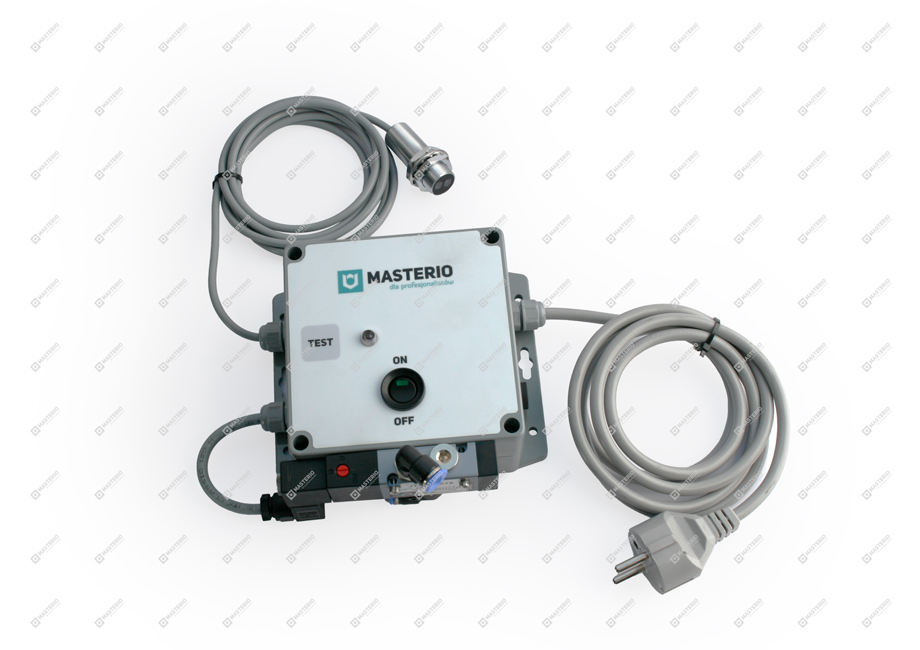
In SN 2 model we introduced two technical solutions, that addressed two biggest flaws of its predecessor. We have implemented a emergency brake mechanism which means that we were able to set the time after which the sensor (in case of a jam or a pause of format under the sensor) will cut off the fluid distribution, which prevents continuous fluid application. Another “technical novelty” was the ability to set the length of application of fluid to a pressure roller. There was also the ability to set on which format the fluid will be sprayed in the glue furnace.
What has not changed was the fact that one system could be used only at one spraying point and that the model could be used at every point of the machine.
Masterio SN 3 spraying system
Masterio SN 3 system was modified to operate two spraying points but one of them had to be the pressure roller in the glue section. We further developed the mechanism responsible for spraying time configuration on the roller, the interval between sprays and the time of application cut off in case of jam or stoppage to prevent fluid overflow on the format. At that point we have redesigned the system, put in reliable parts and stabilized the control system. It made SN 3 a reliable spraying system which operation makes our clients happy.
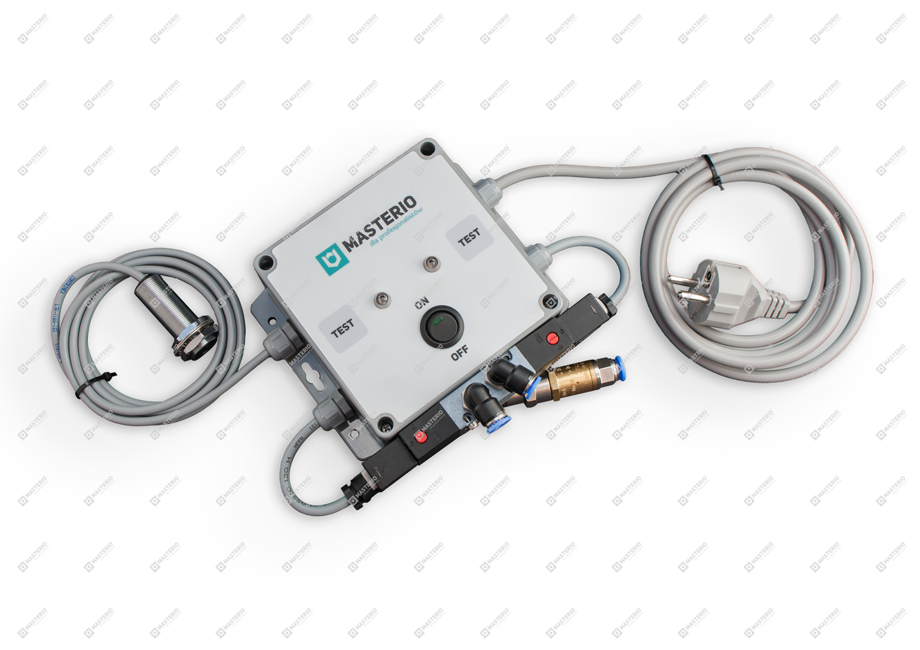
Masterio SN 4 spraying system
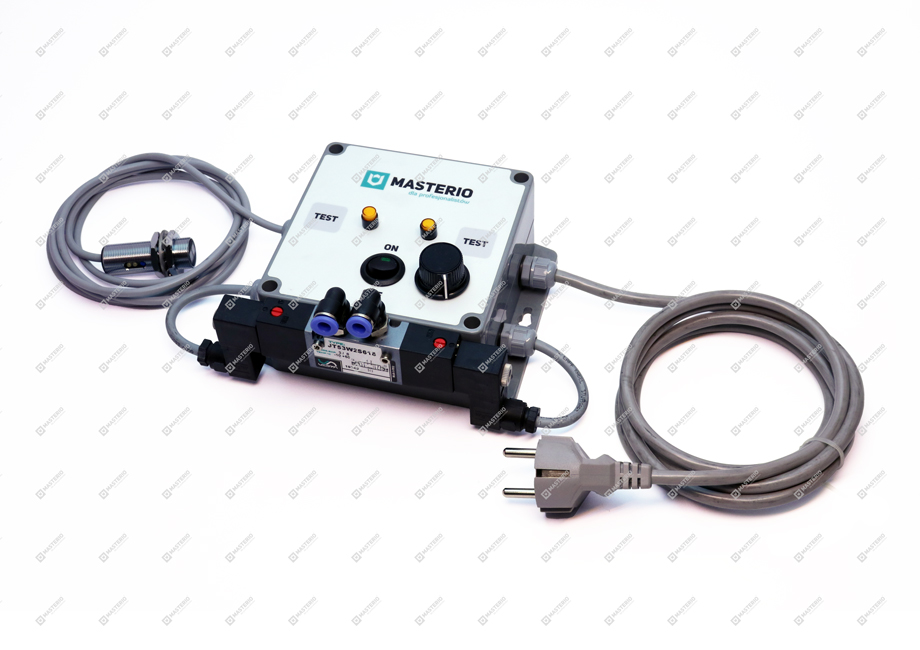
Comparing to its predecessor, this system gained the ability to manually (by operators) set the frequency of OK 20 fluid application on pressure roller sticking the burl on the format (or the roller depending on the spraying fluid nozzle assembly). It was done based on the operators’ opinions, who were expecting greater or lesser moisture on pressure roller(s). In SN 3 model this could be done only by our service personnel because it required internal system programming. By listening to operators’ opinions we introduced a knob that enabled application of OK 20 fluid by request. The system could operate only two spraying points, one of which had to be a point in edge gluing section. All other functions were the same as in SN 3 model.
Masterio SN 5 spraying system
The latest and most advanced system, that has no limits. It was a revolutionary product, and its potential is limited only to the capacity of hard drive installed. The most important change is that the model can operate all four spraying points from one location on the edgebander. The operator can fully regulate spraying time on each nozzle, offset of spraying nozzle opening depending of the format sensor, cut off time and any other combinations necessary. It can also show that the fluid level is low in a container (each of them) in the system or in a given point of the machine. It can calculate working cycles, work time, fluid consumption, send reports or control the fluid requisition.
Masterio SN 5 is an advanced computer for controlling, analyzing and regulating whole spraying system operation, which functions can be expanded upon client's wishes.
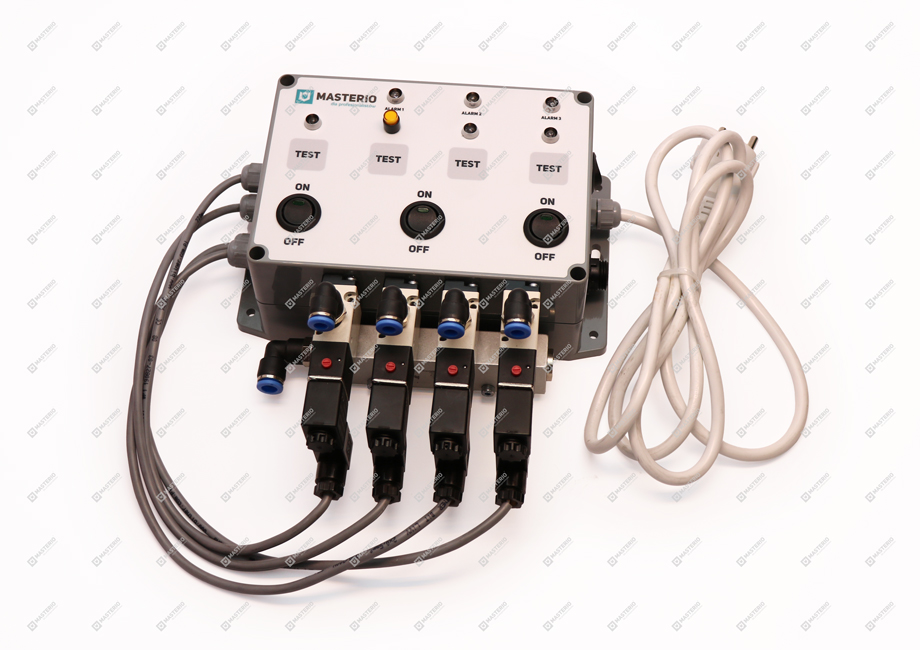
Summary
Based on the above description we hope that you see the point in using Masterio spraying systems and you can answer the question if there is a point of mounting a spraying system on a machine with a factory spraying points.
We have an individual approach to each client, so we can modify every model of spraying system to make our clients happy with the effect.
In case of further questions please do not hesitate to contact us. We will find the most suitable solution for you and will “tailor” the system to your needs.